3D Printing Services
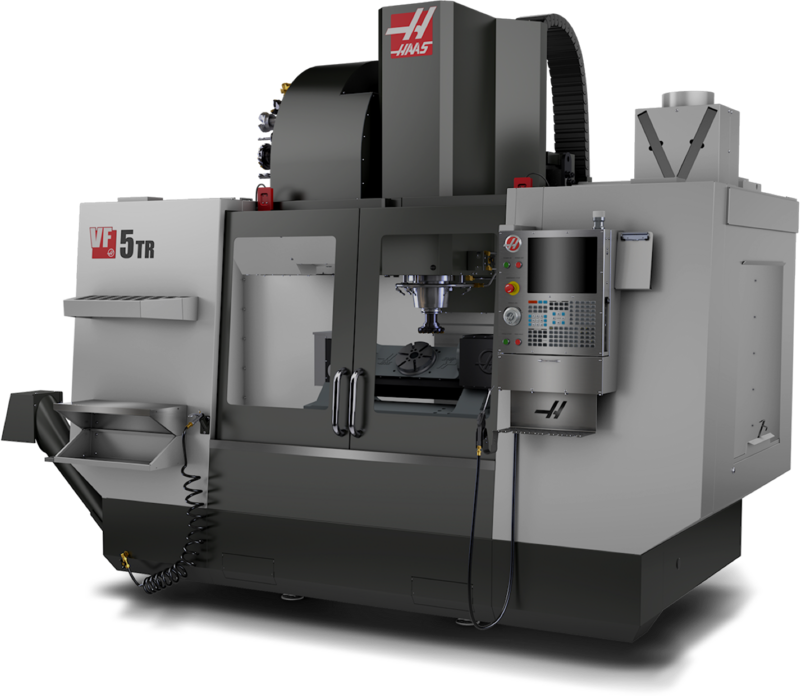
RJM is proud to offer the next generation in adaptive manufacturing, also known as 3D Printing. This technology has accelerated from a method to produce prototypes and one-of-a-kind replacement parts to a preferred manufacturing option for many complicated or highly refined components.
3D Printing is the construction of three-dimensional components from a CAD model (computer assisted design) or a digital 3D model. 3D printing creates objects with materials such as liquid molecules or powder grains that are fused together, typically layer-by-layer.
Just a few years ago, 3D Printing was only suitable for production of prototypes used to help design components that were later manufactured using other techniques. Recently, however, the higher-precision, faster manufacturing cycles and wider range of materials has elevated 3D printing to a viable manufacturing option.
Among materials that are now routinely processed using 3D printing technologies are rigid plastics, aluminum, steel, flexible plastics, titanium, copper, nickel, inconel, cobalt-chromium, tantalum and others.
- The biggest advantage for 3D printing is the ability to produce very complex shapes that are otherwise impossible with conventional manufacturing methods. This includes hollow parts or parts with internal truss structures to reduce weight.
- 3D printed components also offer improved strength, flexibility and resistance to environmental factors.
- 3D printing presents the opportunity to produce a single component as easily as dozens or hundreds.
- The precision of 3d printed components is also quite impressive with manufacturing tolerances that match the most stringent production specifications.
RJM can produce cost-effective prototypes or mass-produced parts using dozens of metals or plastics. We offer numerous high-quality printing processes including:
- FDM (Fused Deposition Modeling) is a common process for early stage prototypes;
- SLS (Selective Laser Sintering) uses high-powered lasers to sinter powdered material, binding it together to create a solid structure;
- SLA (Stereolithography) is known for achieving highly detailed and functionally accurate parts;
- Multi Jet Fusion is a production-grade technology that spreads out a fine layer of powder, deposits a fluid in the desired areas, and then fuses those areas;
- PolyJet is a 3D printing technology similar to inkjet document printing, but instead of jetting drops of ink onto paper, PolyJet machines jet layers of liquid photopolymer onto a build tray and instantly cures them with UV light;
- Other technologies are also available, including Direct Metal Laser Sintering (DMLS), Digital Light Processing (DLP), Electronic Beam Melting (EBM), Laminated Object Manufacturing (LOM), and others.
The phenomenal rise in 3D Printing technology has created a huge demand for products using this manufacturing method. Aside from simple applications such as manufacturing single piece products and gadgets, this method is now used in high-tech industries including medical, aerospace, robotics, electronics, consumer products, automotive and others.
RJM offers 3D Printing Services using four primary materials and methods.
3d Resin Printing is the best option when you need smooth surface, high-quality and detailed components. There are a wide variety of finishing and post processing capabilities.
A number of different resins are available, depending on your needs, including standard resin, gray resin, mammoth resin and transparent resin. All these materials can be used to complete your component or product with swift turnaround times and unparallel quality.
Click for more information on how 3D Resin Printing might work for you.
Polylactic Acid (PLA) is derived from renewable resources like corn starch or sugar cane. PLA is biodegradable and has similar characteristics to polypropylene, polyethylene or polystyrene. It is produced from existing manufacturing methods, making it very cost-effective.
Some common uses include plastic films, bottles, and biodegradable medical devices such as screws, pins, rods, and plates that are expected to biodegrade within 6-12 months.
PLA is popular because it is a cost-efficient, non-petroleum plastic product that is “biodegradable” — naturally degrading when exposed to the environment.
Click for more information on how 3D PLA Printing might for you.